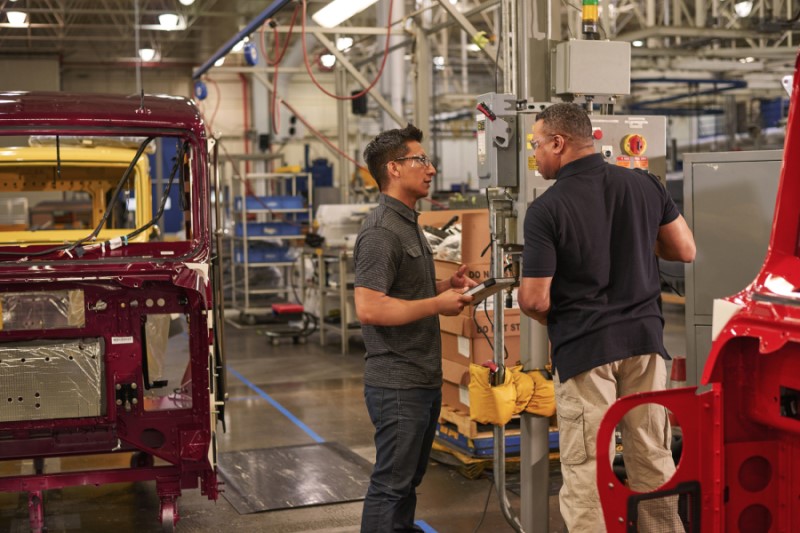
Manufacturers’ digital transformation: A mid-life crisis?
Manufacturing is going through interesting times. It has been roiled by pandemics and wars, seen its supply chains slow down if not completely buckle, and confronted a labor shortage as one generation of workers retires (or quits) and another generation has not yet filled the gap.
Finding a way forward is challenging. But a recent survey conducted for Microsoft by the ARC Advisory Group maps a route that manufacturers can take to navigate a changing world. ARC’s recent report: “The Digital Manufacturing Journey—An ARC Global Analysis.” is based on a survey of over 1,000 Information Technology (IT), Operational Technology (OT), and Engineering Technology (dare I use the acronym “ET”?) decision-makers from North America, Asia, and Europe with deep knowledge of their status and plans for factory digitalization efforts over the next three years. The report makes the strong case that digitalization is key to manufacturers’ success. “Not only are companies faced with changing the number of people needed to do the work,” the report’s authors write. “But they must also rewrite how that work gets done.”1 Greg Gorbach, one of the authors of the ARC Report, has described manufacturers facing a “Digital Transformation Mid-Life Crisis“.
During the ARC Industry Forum 2023 in Orlando, Florida, I had the opportunity to share Microsoft and ARC’s insights from the survey with manufacturers from around the globe.
ZF Group digital transformation journey
Watch the ARC Keynote featuring Gabriel Gonzalez-Alonso, SVP of Production Management, ZF Group Germany, making digital transformation real, relatable, and actionable. Gabriel also generously joined me on the Keynote panel to take questions on ZF Group’s six-year digital transformation journey with Microsoft and PwC for their Digital Manufacturing Platform, which is scaling out to 100 factories over the next year. Gabriel also shared how ZF Group streamlined communications for 110,000 frontline and office workers and is streamlining manufacturing processes with Microsoft Power Platform.
ZF Group is clearly making significant progress on its digital transformation, but for a more sobering look at the ‘broader mid-life crisis’, download the full ARC report for insights and recommendations about kickstarting or accelerating your own digitalization efforts.
Watch my full interview with Greg Gorbach, VP of Digitalization at ARC, for our discussion of the ARC Report. A few key insights and teasers are below:
The Digital Manufacturing Journey—An ARC Global Analysis
Security is still a concern but those in the cloud feel more secure
Securing the cloud rises to the top as the most important challenge when thinking about digital transformation on the factory floor. However, ARC’s primary research conversations have revealed: “those who have made the move to the cloud actually feel more secure.”1
These survey respondents said employee security training (38.2 percent), security monitoring and threat analysis (37.9 percent), and a dedicated security policy (35.9 percent) were essential to digitizing factories. This is especially true as manufacturers build their digital transformation on the cloud, with those in key OT roles showing the most concern about public cloud adoption.
Manufacturers expect security to be ‘built-in’ to the factory platforms and solutions they use for factory modernization.
Sustainability is a top priority
The report notes that we are in a “critical time” regarding taking the steps needed to mitigate climate change. Manufacturers are under intense scrutiny on this count. After all, almost by definition, manufacturing is an asset-heavy, energy-intensive activity. With even more pressure to optimize resources, many manufacturers are already working hard to reduce carbon output and reach low-emission goals. This can be accomplished with the help of software and AI, along with connected machines and workers, digitalization, automation, and the introduction of new operating and business processes.
Respondents were asked about nine factory-level sustainability activities manufacturers can undertake that drive sustainability, such as identifying emissions data to be tracked and accurately collecting carbon data. However, only slightly more than 50 percent of manufacturers have undertaken even one of the nine steps. Only 2.4 percent have completed all nine activities:
- Identify all relevant public reporting standards and requirements.
- Inform plant managers they will be held responsible to achieve factory sustainability targets.
- Identify the specific emissions data to be measured.
- Connect to data sources and accurately collect required carbon data.
- Establish public and internal emissions and energy targets and goals.
- Integrate into financial and other reporting systems.
- Provide visibility into the data and progress towards goals.
- Derive insights and leverage them to create decarbonization action plans.
- Track and manage the progress in executing action plans.
Progress on factory sustainability initiatives was also one of the areas where progress varied dramatically geographically, with Asia leading the way, and North America lagging behind Europe.

European respondents reported the most measurable improvements from digital transformation investments but were more conservative in their plans for digital wins and industrial metaverse investments.
North American respondents claimed the highest cost benefits from digital transformation programs and had a high focus on realizing safety benefits. AI is a key focus for their smart factory investments over the next three years.
Manufacturing executives surveyed in Asia appeared to be further ahead in their factory digitalization efforts, moving workloads to the cloud, and more inclined to work with hyper scalers for their smart factory initiatives.
Manufacturers are making progress on IT, OT, and ET convergence
Much is written about IT and OT convergence, but ET decision-makers were added to the mix for this survey.
IT is more optimistic than its OT counterparts about moving to the public cloud over the private cloud. OT still has a higher concern about security and latency and moving workloads to the public cloud. IT feels more comfortable with some of the unknowns, such as edge technologies moving to the private versus public cloud. These findings highlight the further opportunities for IT and OT to cross-pollinate their experiences, align, understand each other, and determine what needs to be prioritized.
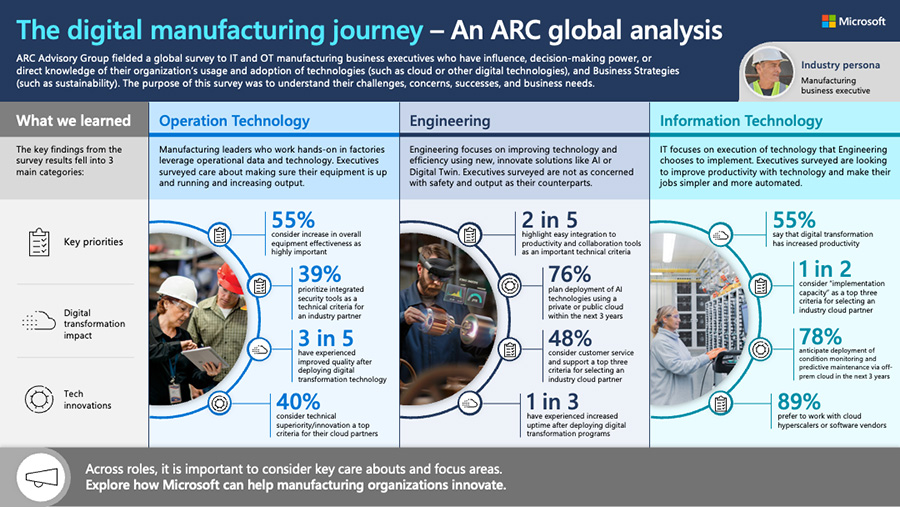
Engineering respondents focus more on improving technology and efficiency using new, innovative solutions like AI or Digital Twin than their IT and OT counterparts. Engineering also led the way in expressing the need for easy integration of purchased technology solutions with standard office collaboration and productivity tools.
Microsoft Cloud for Manufacturing can help you achieve more
Download the full report for ARC’s insights on key technical requirements for modern factory solutions, and recommendations on how to:
- Advance your digital transformation journey.
- Select and prioritize your transformation target areas.
- Understand cybersecurity and how to secure your factories.
- Leverage the different skills across the complex manufacturing ecosystem.
- Use technology to empower the frontline workforce.
Learn more
Sign up to receive updates about Microsoft Cloud for Manufacturing and reach out to your Microsoft sales representative for expert support.
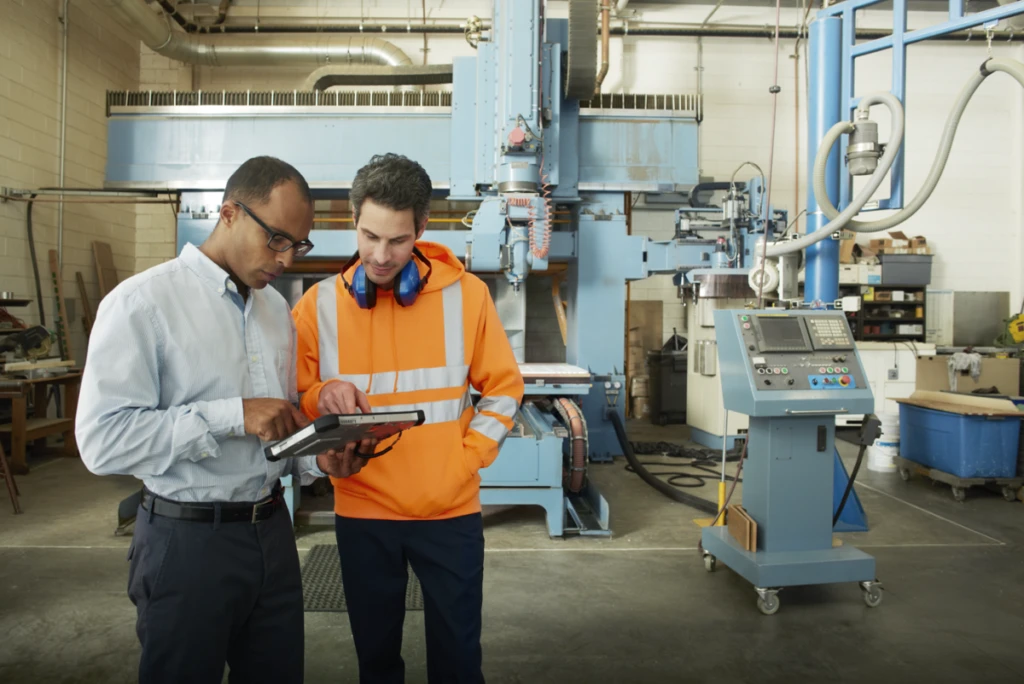
Microsoft Cloud for Manufacturing
Empower your workforce with smart manufacturing solutions.
1The Digital Manufacturing Journey—An ARC Global Analysis, ARC White Paper, December 2022.