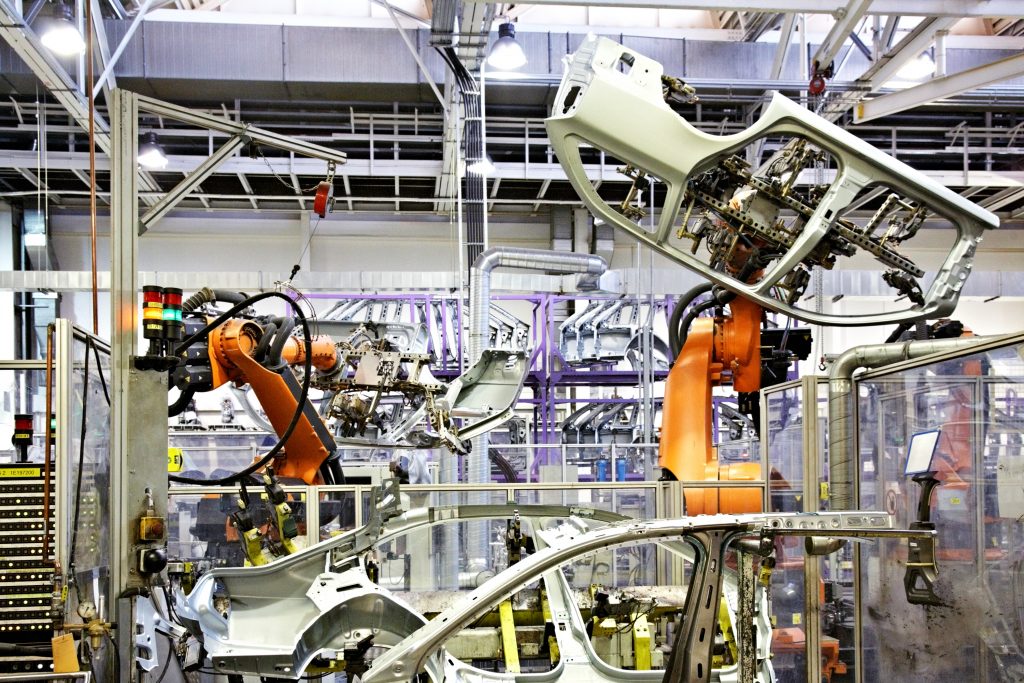
Bringing cloud intelligence to the edge in connected factories
The Industrial Internet of Things is empowering manufacturers with end-to-end insights into their production. In the past, live operational data was transmitted from connected industrial devices to the cloud, where AI services derived insights from the data. This pattern excluded many customers who have disconnected or partially connected devices, who need to respond in real time to insights, or who simply want to reduce the bandwidth costs incurred by transferring terabytes of raw data to the cloud. Azure IoT Edge solves these problems and enables all customers to benefit from the Industrial Internet of Things (IIoT) by bringing high-value cloud services down to edge devices.
Colin Masson, Microsoft’s Global Industry Director for Manufacturing Solutions, sat down with Erich Barnstedt, Principal Software Engineering Lead, and Chipalo Street, Azure IoT Principal Program Manager, to discuss the benefits of edge computing for manufacturers.
Colin Masson: What is Microsoft Azure IoT Edge, and how does it facilitate Connected Manufacturing scenarios?

Chipalo Street, Azure IoT Principal Program Manager, Microsoft
Chipalo Street: Azure IoT Edge is one of Microsoft’s edge computing offerings. Edge computing is the processing and analysis of data on premises, at the edge of the network, close to the sources of data. This is a capability that is applicable to many industries, especially manufacturing and other heavy industries.
Erich Barnstedt: Consider, for instance, an oil rig with connected devices. The operators of the oil rig collect sensor data from the drill and feed that data through analytics to determine if the drill will be damaged soon. They need to make a very quick decision to shut off the drill if it is forecasted to be damaged; a delay of even a few seconds could have very serious consequences. In the past the analytics to predict damage has only run in the cloud. This means that, at a minimum, data must flow
from the devices, to the cloud, and have insights or actions sent back down to the devices.
Azure IoT Edge allows these cloud services to be run locally, offering the oil rig instantaneous response times, so performance-critical decisions can be made in milliseconds rather than seconds. All processing happens locally, eliminating the latency incurred by sending data to the cloud, processing it, and then sending the insights back to the edge. Azure IoT Edge also ensures that data analysis continues even when the Internet connection is intermittent.

Erich Barnstedt, Principal Software Engineering Lead, Microsoft
In this scenario, the oil rig operators run data through machine learning and stream analytics at the edge, but they also see cloud benefits. After uploading data to the cloud, they leverage cloud-based tools to optimize the statistical models used at the edge. The aggregated data enriches the statistical models, making them more accurate, and an executable copy of the models is downloaded to the edge to analyze live data.
Colin Masson: Are there other scenarios where Microsoft Azure IoT Edge can augment cloud computing?
Chipalo Street: Safety-critical systems always need to happen on premises. You need to know that these systems will operate or fail in a safe state regardless of what happens to the cloud or the connection. The simplest on-premises approach is having the big red shut-off button on each machine.
Azure IoT Edge enables a more complex safety system. Say that you’re monitoring the temperature across a range of machines. You need to shut them all down if the combined temperature gets too high to prevent damage to the machines and risk to human operators. In this scenario, a safety system at the level of the individual machine is not enough, because it can’t track combined temperature across multiple machines. Your safety system needs to be one level higher to monitor and control multiple machines, and you can do this with Azure IoT Edge.
Colin Masson: What would you say are the key benefits of Microsoft Azure IoT Edge?
Erich Barnstedt: A ton of new scenarios are enabled by the ability to run AI, that formerly only lived in the cloud, on local devices. Machine learning can now be used in IoT scenarios that require real time responses. Performance of solutions can be increased by eliminating the time it takes to transmit data to the cloud and back, you achieve close to instantaneous data analysis, which is vital to making critical operating decisions.
Mission and safety critical IoT solutions are now resilient to internet connectivity. Azure IoT Edge enables devices to continue operating and transmitting data for analysis even offline, ensuring reliable production even with intermittent internet connectivity.
Finally, IoT solution costs are decreased. Transmitting all your data to the cloud can be expensive, especially if you have facilities in remote places where internet access is expensive. By doing your analysis at the edge, you reduce the amount of data that you need to send to the cloud.
Colin Masson: How does Azure IoT Edge address manufacturers’ data security and compliance concerns?
Chipalo Street: Azure IoT Edge has a robust security framework that can protect against a wide range of risk profiles and deployment scenarios. Additionally, Azure IoT Edge can be extended with custom code that is tailored to individual solutions. This extensibility is necessary to secure and protect data on all kinds of devices.
Notably, Azure IoT Edge enables manufacturers to sanitize local data before sending it to the cloud. For instance, manufacturers can remove personally identifiable information to comply with government regulations that restrict transfer of that data. Running AI locally allows analysis of data that could not have been sent to the cloud. This means manufacturers see the benefits of analysis without compromising data security or compliance. It is also worth noting that we recently open-sourced Azure IoT Edge.
Colin Masson: How does Azure IoT Edge lay the groundwork to transform the factory of today into the factory of the future?
Erich Barnstedt: I recently read an article published by acatech, “Industry 4.0 Maturity Index,” that describes six phases of transformation required to achieve the factory of the future: computerization, connectivity, visibility, transparency, predictive capacity, and adaptability. Azure IoT Edge lays the groundwork by enabling connectivity, but its benefits don’t stop there.
The question is: How can a factory achieve a self-optimizing system that guarantees uptime with autonomous responses? That’s adaptability, the final phase of this maturity index. Azure IoT Edge sets the stage for this with its modular architecture. Manufacturers download so-called containers of executables to the edge and run them either in parallel or in sequence. This flexible architecture enables visibility and transparency right at the edge.
It also facilitates capabilities like automatic triggering of alarms based on thresholds. Say you’re monitoring the pressure on one of your machines. The pressure keeps rising until it reaches a threshold and the system triggers an alarm and provides a mitigation option to the user. The user clicks a button to open the release valve on the machine. This scenario is possible with the Azure IoT Connected Factory solution accelerator and Azure IoT Edge.
Chipalo Street: You can take this one step further by applying a machine learning model. The model identifies that the past hundred times the pressure has increased at this rate, it reached the threshold within two hours of this point. There’s no need to wait two hours—instead the system opens the valve now, preventing potential damage to the machine. Now the machine is part of a self-optimizing or self-healing system.
Colin Masson: Thanks for talking us through some of the intelligent edge and intelligent cloud scenarios that are powering the factory of the future!
Start your journey to the factory of the future with the Microsoft Azure IoT Connected Factory solution accelerator. To learn more, check out our solution demo, or contact us today to discuss what Microsoft Azure IoT Connected Factory could look like for your business.