The Internet of Things gives the world’s cities a major lift
https://youtube.com/watch?v=ZBGKgiKQfeY
With city populations exploding, city planners and builders have critical problems to solve. To make room for 3 billion people to live, work and play, planners know that the best direction to go is up. Keeping elevators running smoothly is key; in buildings that soar to more than 1,000 feet, taking the stairs is simply not an option. Easing the flow of people through towering, high-capacity mega-structures is critical to the quality of life in cities; crowded lobbies are the traffic jams of the future.
By 2050, seven out of 10 people will live in cities — a staggering 3 billion more than today, according to the World Health Organization.
Big cities can’t exist without skyscrapers, and in turn, skyscrapers can’t exist without elevators. ThyssenKrupp Elevator is one of the world’s leading elevator manufacturers, specializing in innovative and energy-efficient products. It maintains more than 1.1 million elevators worldwide, including those at some of the world’s most iconic buildings.
New York’s One World Trade Center (center) boasts 73 ThyssenKrupp elevators, some of the fastest in the Western hemisphere.
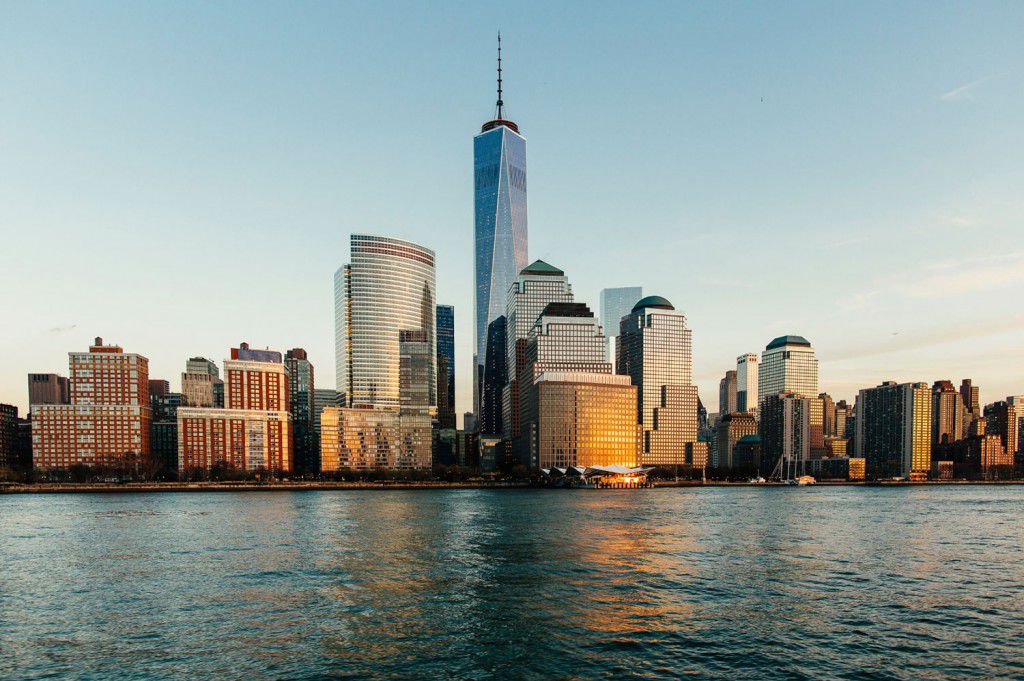
TK1 – NYCskyline-th-1024×68
At New York’s brand-new 102-story One World Trade Center ( no link)— the tallest building in the Americas at 1,776 feet — ThyssenKrupp’s elevators will carry an estimated 3.5 million people every year. Traveling at 23 miles an hour, the building’s elevators are the fastest in the Western Hemisphere, going from the bottom to the top in just 60 seconds, on 198 miles of steel cable.
In Riyadh, Saudi Arabia, at the 1,263-foot CMA Tower— the country’s tallest skyscraper and one of the tallest all-office towers in the world — ThyssenKrupp’s elevators serve 5,500 workers, using an advanced shuttle system and touchpads that direct elevator traffic.
And in China, a steadily growing volume of passengers led to long elevator lines at the five-star Bayshore Hotel in Dalian — until ThyssenKrupp installed a system of new elevators that can carry significantly more passengers per hour.
ThyssenKrupp wanted to gain a competitive edge by focusing on what matters most to its customers in buildings the world over: reliability. Drawing on the potential of the Internet of Things (IoT) by connecting its elevators to the cloud, gathering data from its sensors and systems and transforming that data into valuable business intelligence, ThyssenKrupp is vastly improving operations — and offering something its competitors do not: “We wanted to go beyond the industry standard of preventative maintenance, to offer predictive and even preemptive maintenance,” says Andreas Schierenbeck, ThyssenKrupp Elevator CEO, “so we can guarantee a higher uptime percentage on our elevators.”
To do this, ThyssenKrupp teamed up with Microsoft and CGI to create a connected, intelligent line-of-business asset monitoring system that raises elevator reliability to new heights. The solution brings together technologies at the heart of Microsoft’s platform for the Internet of Things.
“When you really think about it, it’s really the Internet of Your Things,” said Microsoft CEO Satya Nadella at the 2014 Worldwide Partner Conference. “So when you’re talking to a customer, they have these things in the field, and for the first time now, in a cost-effective way, they can put a computer on them and get data back from them so that they can reason over it. Now that all sounds great, but for what purpose? The purpose is of course business model transformation.”
Fix it — before it breaks
CGI is the world’s fifth-largest independent IT and business process services firm, specializing in high-end business and IT consulting, systems integration, application development and more. CGI developed a solution that securely connects ThyssenKrupp’s “things” — the thousands of sensors and systems in its elevators that monitor everything from motor temperature to shaft alignment, cab speed and door functioning; the data they gather; and PCs and mobile devices used by its workforce of technicians — to the cloud with Microsoft Azure Intelligent Systems Service.
Technicians at ThyssenKrupp’s call center in Seoul, South Korea share the same real-time view of data as field technicians all over the world.
ThyssenKrupp can now use the Intelligent Systems Service to capture that data, transmit it into the cloud and combine it into a single dashboard that serves up two basic types of data: alarms that indicate an immediate issue, and events, which are stored and used for management. “This is a difference in time criticality, and Intelligent Systems Service handles both, which is important,” says John Hicklin, principal Internet of Things consultant for CGI. The solution provides technicians instant diagnostic capabilities, using Power BI for Office 365 for rich, real-time data visualization — a powerful new tool in ThyssenKrupp’s maintenance arsenal.
Now, instead of just reacting to a failure alarm, technicians can use real-time data to define a needed repair before a breakdown happens. And, thanks to a two-way flow of data, technicians can remotely put an elevator into diagnostics mode, or they can send it to another floor. It all adds up to less time traveling, better efficiency and reduced costs.
Technicians access predictive data from elevators on mobile devices, including error codes, their probable causes and likely fixes.
The virtual troubleshooter
CGI’s solution also seeks to take much of the guesswork out of repair work. With Microsoft Azure Machine Learning(Azure ML) service, ThyssenKrupp has an unprecedented view into elevator operations and maintenance now — and in the future. The system contains an intelligent information loop: Data from elevators is fed into dynamic predictive models, which continually updates datasets via seamless integration with the Intelligent Systems Service.
“I call it the ‘virtual troubleshooter,’” says Rory Smith, director of strategic development for the Americas at ThyssenKrupp Elevator. “When the elevator reports that it has a problem, it sends out an error code and the three or four most probable causes of that error code. In effect, our field technician is being coached by this expert citizen.”
Now, the elevators can actually teach technicians how to fix them, thanks to the Microsoft Azure Machine Learning service. With up to 400 error codes possible on any given elevator, that “coaching” can significantly sharpen efficiency in the field. Smith expects the predictive models will continually improve with time as more and more datasets are fed into the system. The result? Dramatically increased elevator uptime.
ThyssenKrupp’s use of machine learning for predictive analytics puts the company at the leading edge of an important trend. According to Gartner*, “The rapid growth in available data, particularly new sources of data — such as unstructured data from customer interactions and streaming volumes of machine-generated data — require greater levels of sophistication from users and systems to be able to capture their full potential.” Harnessing the potential of ThyssenKrupp’s elevator-generated data is leading directly to greater business intelligence from what Gartner calls “‘non-data-scientist-friendly’ tools” — and happier customers.
As new datasets are fed into the predictive models, ThyssenKrupp expects to see lower maintenance costs and increased reliability and uptime.
A flexible solution
CGI relies on the flexibility of Microsoft technologies, Hicklin says: “Azure is quite inclusive, in terms of things that it’s able to host, and the Intelligent Systems Service is inclusive in terms of devices it can connect with. If you put those two things together, you have a very rich cloud environment that is enterprise-ready, and also the ability to deal with the real world and with different types of devices and applications.”
By focusing on data, and enhancing datasets with rich analysis and predictive modeling, the Internet of ThyssenKrupp’s Things is giving the company a competitive edge, transforming maintenance operations, creating new efficiencies in workflow, cutting operating costs, increasing elevator uptime — and giving the world’s burgeoning cities a lift they can rely on.
*Gartner, Magic Quadrant for Advanced Analytics Platforms, Gareth Herschel, Alexander Linden, Lisa Kart, February 19, 2014