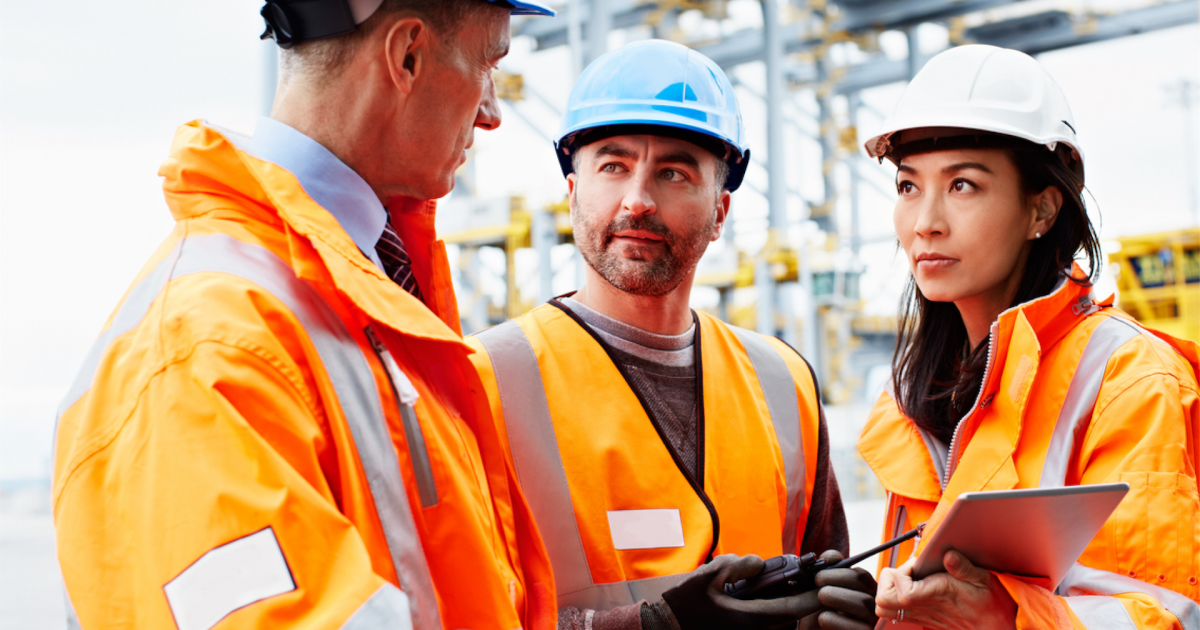
Intelligent field service at Hannover Messe
As the manufacturing marketplace continues to evolve, so do customer expectations. Customers expect faster and faster response times and improved asset availability. To meet these growing demands, manufacturers need to transform field service to increase efficiency and ensure a first-time fix. Today’s average first-time fix rate is 74 percent, which means over 25 percent of service calls require return visits, which can cost upwards of $1,100 per truck roll., according to an article in Field Technologies Online. Return visits also mean dissatisfied customers, broken SLAs, frustrated technicians, and wasted time and resources.
Remote monitoring of assets is the first step for manufacturers to leverage the Internet of Things (IoT) to increase operational efficiency and improve profitability. Operational data, provided through remote monitoring, enables field service to deliver quick response times and improve first-time fix rates.
Connected field service is the next step in the journey to transform field support. Connected field service enables organizations to transform service from a costly break-fix model to a proactive and predictive service model through the combination of IoT diagnostics, scheduling, asset maintenance, and inventory on the same platform. It is the foundation of a seamless service process that can increase customer satisfaction and boost revenue.
Want to improve visibility and field operations? Let me tell you a story.
Swiftel International is a telecommunications firm specializing in electronics payment solutions. Swiftel needed greater visibility when it came to device management and field operations. Device malfunctions demanded time-consuming inspections and scheduling field technicians was difficult due to blind spots in the company’s performance tracking and work scheduling. Swiftel wanted to:
- Streamline remote device tracking and troubleshooting
- Monitor field technician performance and leverage technicians with the right training
- Improve customer satisfaction with greater service visibility
Collaborating with Microsoft, Swiftel chose a comprehensive solution of Microsoft Dynamics 365 for Field Service and Azure IoT. This approach would allow asset tracking and scheduling in the field with the flexibility of cloud access. Swiftel would also be able to optimize technician schedules, track inventory, and perform advanced data analysis for efficient routing and technician skill-matching.
Fast forward to streamlined services and enhanced productivity.
Now Swiftel can manage its devices remotely, and schedule better and manage logistics more effectively. Swiftel has a more comprehensive view of workers in the field, and has increased productivity and lowered costs due to more streamlined services.
Swiftel uses this intelligent system to optimize technician assignments using multiple factors, such as a technician’s experience in handling the specific failure, the customer’s preferred technician or the technician’s proximity to the site. Leveraging machine learning, Dynamics for Field Service automatically assigns the work order to the most experienced available personnel.
As the volume of requests increase, this system optimizes the technician’s schedule to create the most efficient travel path, allowing the technician to perform additional calls that day. Real-time inventory management ensures that the replacement part is available on the scheduled date and that the technician has access to the tools needed to complete the job. Dynamics for Field Service can identify the right parts to replace, where they should be purchased, and provides more accurate lead time predictions for the organization.
Let’s take our story even further. What if a technician needs additional help during the service call? They can leverage Dynamics 365 Layout and Dynamics 365 Remote Assist using HoloLens. This emerging technology offers technicians 3-D renderings overlaid directly onto the device, highlighting the parts needing repair while displaying performance data—even on a mobile device. Artificial intelligence (AI) can use the data from predictive analytics to make just-in-time recommendations to the technician, ensuring repairs are completed correctly the first time, every time. Remote Assist is in the early phases of being used to improve safety and reduce costs through the use of remote experts for equipment verification and incident response.
Let’s get back to our story. Now Swiftel technicians can commit repairs to a device with minimal downtime, and the device is fixed right the first time by the best technician available. Check out the full Swiftel case study for more information.
Create your own story at Hannover Messe
Make your field service dreams come true by experiencing Dynamics 365 for Field Service, and Dynamics 365 Remote Assist, using Hololens, and learn how connected field service works. Join me for a personal tour of these technologies in booth #40 at Hannover Messe on April 1 – 5 in Hanover, Germany.
You’re invited to learn how Microsoft Dynamics 365 Business Applications can transform your support operations. Try mixed reality and Hololens and see for yourself how AI can proactively drive efficiencies, optimize resources and modernize field service. Find out how easily you can leverage connected devices and IoT with Field Service to deliver proactive and never fail service to your customers.
I look forward to seeing you at Hannover Messe!